Drum granulator is one of the most widely used equipments in compound fertilizer production. The main working mode of the drum granulator is wet granulation. Through a certain amount of water or steam, the basic fertilizer can be fully chemically reacted after being humidified in the cylinder. Under certain liquid phase conditions, with the help of the rotary motion of the cylinder, the material particles are squeezed and agglomerated into balls.
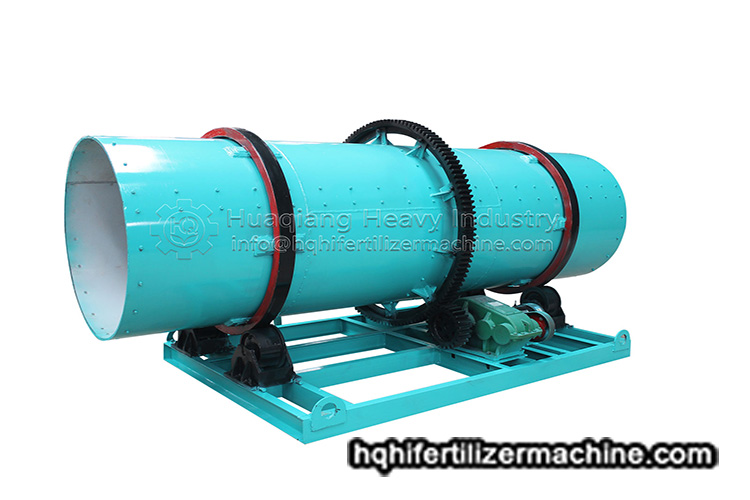
The working principle of the drum granulator: the material enters the front end of the rotating cylinder from the feeding pipe (the slope of the feeding pipe is greater than the natural inclination angle of the material) and the steam inlet pipe at the front end of the cylinder ejects water steam with a certain pressure. The nozzle of steam inlet pipe is located at the bottom of material. And the steam has a certain pressure. Therefore, the material can obtain some moisture evenly and form small particles. Because the cylinder has a certain slope. Under the action of gravity and friction force of lining plate, these small particles continuously move in the circumference and axis direction of the cylinder, and in the movement, the smaller particles gradually form particles of certain specifications.
Performance characteristics of drum granulator
1. The technical innovation, structure improvement, reasonable process layout, advanced technology and low production cost of drum
fertilizer granulator machine are introduced.
2. The drum granulator has the characteristics of high wear resistance, convenient maintenance, high ball forming strength, good appearance quality, corrosion resistance, wear resistance, low energy consumption, long service life and convenient operation and maintenance.
3. The
granulator machine for fertilizer has high pelletizing rate and drying efficiency, and the pelletizing rate is up to 90%. There is a small amount of returned material, and the particle size of the returned material is small, so it can be granulated again; steam is used to heat the material to improve the material temperature.
4. Reasonable layout, advanced technology, small power, no three waste emissions, stable operation and convenient maintenance.