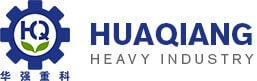
1.Compound fertilizer equipment granulation process and equipment characteristics
Conventional granular fertilizer production methods: Conventional granular fertilizer production methods are divided into extrusion method and agglomerate method. Extrusion granulation uses ring mode, flat mode and roller granulator. During the granulation process, the ring die and template are worn out, the service life is short, the equipment maintenance cost is high, and the power consumption is also large. The particles are cylindrical or flat, with poor fluidity and are not suitable for mechanized fertilization. Agglomerate granulation mostly uses disc granulator and drum granulator, which pulverize dry organic raw materials and fertilizer into fine powder, and then use disc granulator or drum granulator to roll the material into granules.
2.Compound fertilizer equipment processing organic fertilizer
Although it is organic fertilizer, compound fertilizer equipment is also suitable for the processing of such products. First, ferment the organic raw materials such as feces. During this period, the fermentation period can be shortened by adding fermentation bacteria. If the material has large moisture content, you can use a dehydrator to reduce the moisture content, or mix with dry straw powder to reduce the moisture to the optimum range of fermentation requirements, so that the animal manure can be completely decomposed in about 2 weeks. Then the pretreated raw materials can be put into the organic fertilizer granulator equipment such as the disc granulator for production. The inclined disc rotates continuously, and the powdered material gradually rolls into granules. Due to the high moisture content of the produced granular fertilizer, dryers, coolers and other organic fertilizer equipment are still needed to reduce the moisture content of the particles, so as to prevent agglomeration caused by stacking pressure after packaging and storage. In order to improve the productivity of the dryer, models with larger diameter and length are usually selected to increase the effective volume of the drum and extend the drying time of the material. Dryers of different specifications must be equipped with matching oil (coal) furnaces for heating and induced draft fans with corresponding air volume. In addition, if the fertilizer contains active microorganisms, the temperature of the hot air entering the drum dryer should not be too high. Determining the optimal hot air temperature and the storage time of materials in the drum dryer through experimental research has become the key to improving drying efficiency and reducing equipment investment.