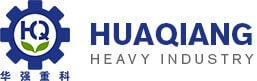
Why are fertilizer factories keen to choose a pair-roll extrusion granulator for granulation? This is because the pair-roll extrusion granulator is the "universal fertilizer granulator machine" in the production of fertilizer granulation. The structure of the pair-roll extrusion granulator is divided into There are three parts: granulation, crushing and screening. The whole machine is made of carbon steel structure, and the squeeze roller is made of 20 chromium manganese titanium and other special wear-resistant materials.
The roller granulator is granulating equipment. It is produced by non-drying room temperature process, one-time molding. The equipment has low investment, quick results and good economic benefits. The complete set of equipment has a compact layout, scientific and reasonable, and advanced technology. Energy saving and consumption reduction, no three wastes are discharged, stable operation, reliable operation and convenient maintenance. The raw materials have wide adaptability, suitable for the granulation of various raw materials such as compound fertilizer, medicine, chemical industry, feed, etc., and the product granulation rate is high.
The advantages of the roller extrusion granulator model are low cost, stable output, adapt to various organic fertilizers, compound fertilizer, compound fertilizer granulation, and eliminate the conventional steps of drying and cooling. It is an ideal starting point for small enterprises.
However, the roller extrusion granulator also has its shortcomings. After the granulation, the appearance of the granules is not very round and there are corner burrs. If the requirements for the shape of the finished product are very strict, a rounding machine can be added.
The advantages of the roller extrusion granulator machine for fertilizer:
1. Energy-saving and consumption-reducing extrusion granulation means that the material is granulated at room temperature. Compared with other methods, it does not require drying measures such as fuel oil and gas.
2. No need to add additional binder, the commonly used domestic production method of compound fertilizer is steam granulation. After the water vapor condenses and crystallizes between the material molecules, it acts as a binder in the manufacturing process. However, in the drying process, the water inside and on the surface of the particles must be driven out; otherwise the fertilizer will easily stick and agglomerate during storage. However, dry granulation does not require additional additives, only uses the intermolecular force of the material itself, which simplifies the process and reduces energy consumption.
3. Lower investment because the drying process is omitted, and the return ratio is low (accounting for about 15% of the total feed volume of the extruder), the process flow is simple and the investment is low.
4. The composition of raw materials is flexible. Extrusion and granulation have a wide range of raw materials. At present, there are more than 20 kinds of materials that have been successfully used for extrusion and granulation: ammonium nitrate, urea, ammonium chloride, calcium nitrate, potassium chloride, and sulfuric acid. In addition, the extrusion granulation process can flexibly realize the replacement of product formulas in a very short time, and a set of equipment can produce products with more than 30 formulas.
5. Green and environmentally friendly, there is no three wastes emissions, and the capacity of extrusion granulation consumption is only electricity, and there are no three wastes emissions for environmental protection. It adapts to * the basic national policy on environmental protection and is also in line with the development strategy of corporate environmental protection.