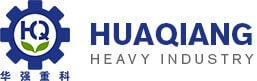
Proper pressure adjustment in double roller press granulators is crucial for achieving quality pellets, and material characteristics play a key role in determining the optimal pressure settings.
1. Material Moisture
High Moisture
Wet materials are naturally more moldable. Reduce pressure to avoid clogging the machine or deforming pellets. High pressure turns sticky materials into a paste between the rollers of a double roller press granulator.
Low Moisture
Dry, loose materials need higher pressure to bind properly. Insufficient pressure leads to weak pellets that crumble easily.
2. Material Stickiness
Sticky Materials
Naturally adhesive materials require less pressure. Too much force creates rough pellet surfaces and speeds up equipment wear.
Non-Sticky Materials
These need extra pressure to form stable pellets. Low pressure results in loose, fragile granules.
3. Particle Size
Fine Powders
Fine-grained materials are easy to squeeze, but in order to ensure the compactness of the particles, the pressure needs to be adjusted according to other characteristics of the material. If the viscosity of the fine-grained material is high, the pressure can be appropriately reduced. If the viscosity is low, the pressure needs to be appropriately increased.
Coarse Materials
Large particles demand maximum pressure to lock them together. Weak compression leaves gaps, producing irregular or broken pellets.
Only by accurately grasping the characteristics of the material such as moisture, viscosity and particle size, and reasonably adjusting the pressure of the double roller press granulator, can high-quality granular products be produced.